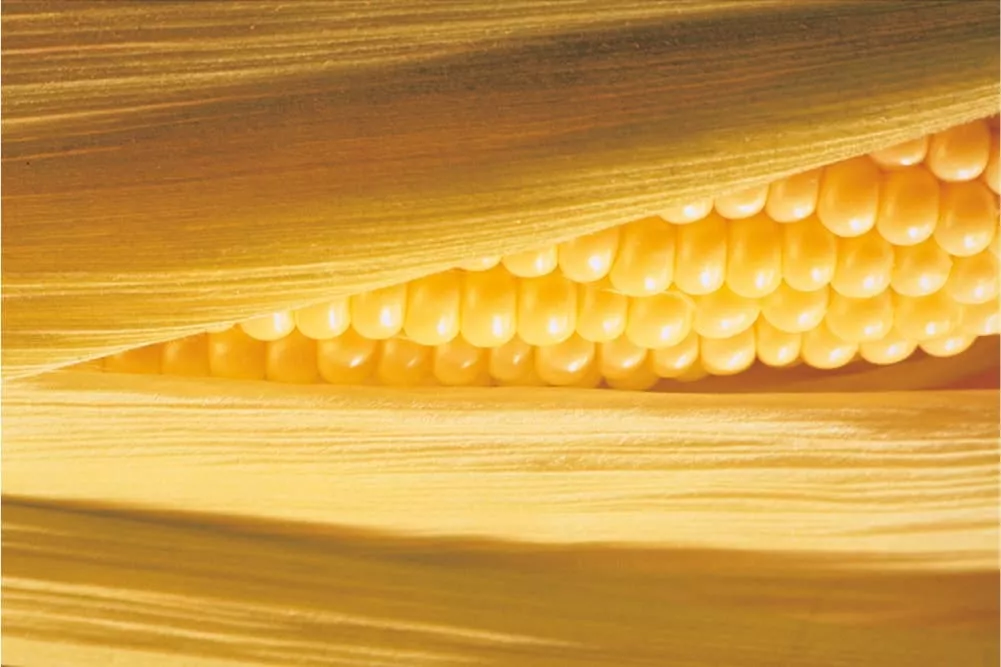
Our approach:
We source corn, our core raw material, regionally to support local agriculture and reduce transport emissions. Our strategy includes partnerships that promote sustainable agricultural practices.
Our progress:
We engage with long-term, trusted suppliers to ensure a compliant, stable and reliable supply chain, and work with them to collect primary GHG emissions data, enabling more precise product carbon footprint calculations. We aim to promote regenerative agricultural practices that preserve and improve soil health, biodiversity, climate, and water while at the same time supporting livelihood of farmers and surrounding communities.
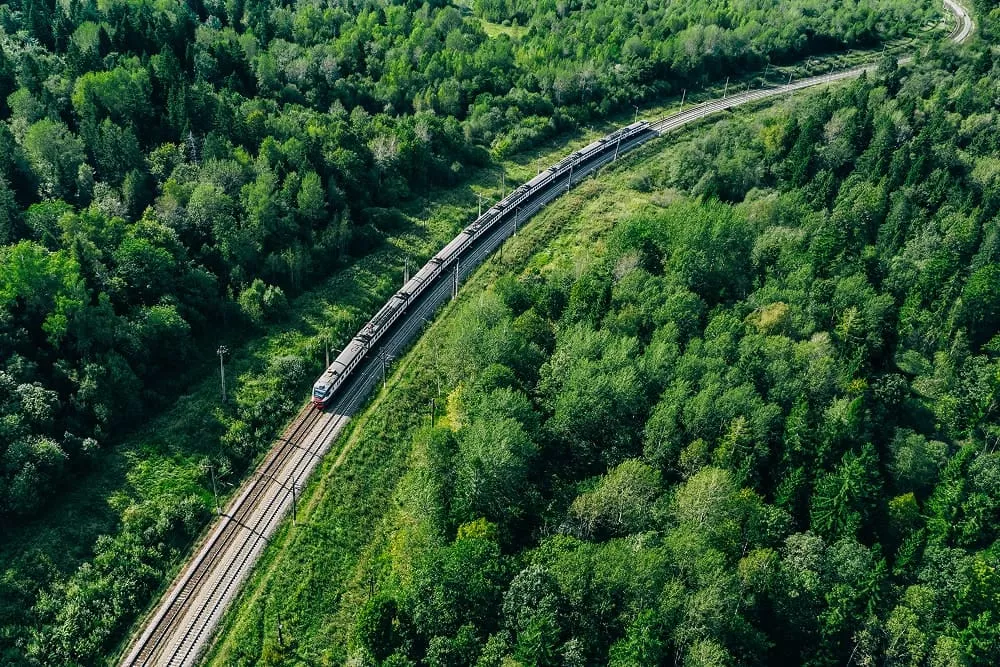
Our approach:
We integrate sustainability principles into our shipping and logistics by prioritising local sourcing and emission efficient transport modes wherever possible. Our strategy focuses on minimising environmental impact while ensuring reliable, efficient delivery to our customers.
Our progress:
We work closely with our suppliers, customers and logistical partners to minimise goods transport distances and maximise rail and river usage for continental transport in order to minimise greenhouse gas emissions. Furthermore, we use bulk deliveries whenever possible in order to avoid packaging waste, and we apply a strict airfreight-by-exception policy.

Our approach:
We integrate sustainability into every stage of our manufacturing processes, ensuring environmental stewardship while supporting safe, fair and thriving working conditions for all. Our goal is to balance operational efficiency with a positive impact on people, climate, and nature.
Our progress:
We transform renewable feedstocks into safe and biodegradable products through biotechnological processes like fermentation, while minimising waste through the generation of valuable by-products next to the intended products. This strategy makes our business model intrinsically circular.
We invest in energy efficiency and transformation to mitigate climate change, improving continuously our energy management systems, electrifying our production processes and producing ourselves biogas and renewable electricity to reduce greenhouse gas emissions.
We strive to reduce continuously our water withdrawals through water-saving initiatives and to ensure systematic compliance of our own wastewater treatment plants.
We maintain a strong commitment to the health, safety, and wellbeing of our employees. Through training, dialogue, and robust safety measures, we create an inclusive and respectful work environment that supports long-term development and engagement across all our sites.
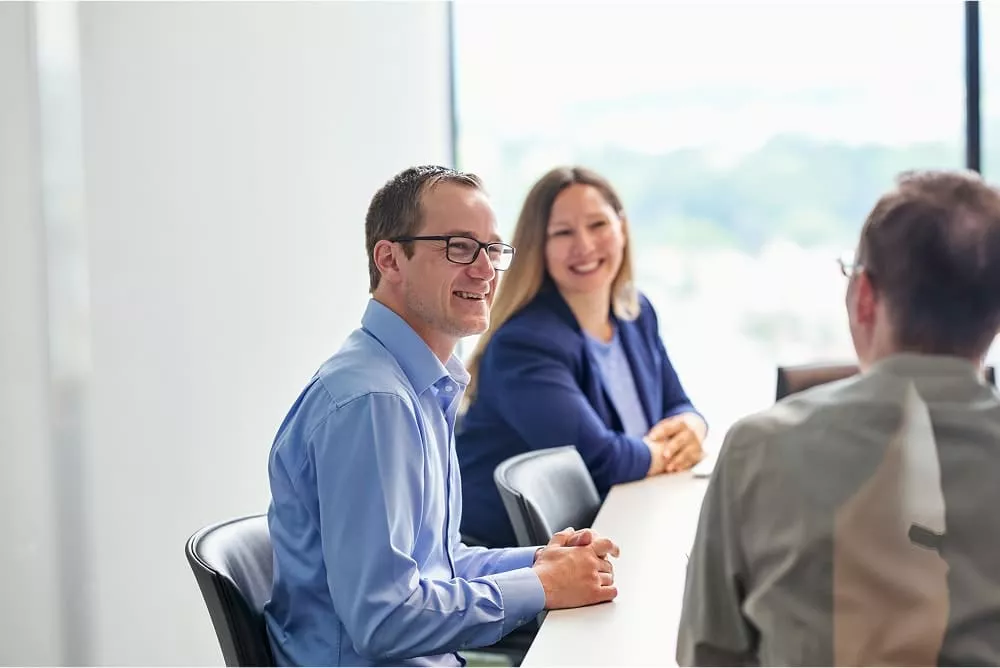
Our approach:
Sustainability is a core element of our value proposition, embedded in product development, sourcing, manufacturing, marketing, and customer engagement. We connect with our customers to ensure that our sustainability initiatives meet their needs and allow them to reach their own sustainability goals.
Our progress:
We align our sales efforts with market trends, offering products that address customer needs for sustainability and innovation. Our team actively listens to customers, fostering ongoing knowledge exchange and providing tailored insights and support from dedicated sustainability experts, including product carbon footprints, to help them reduce their environmental impact. Through transparent sustainability reporting and participation in leading ESG rating platforms, we ensure that our customers can make informed decisions when deciding about their first choice for our sustainable solutions.
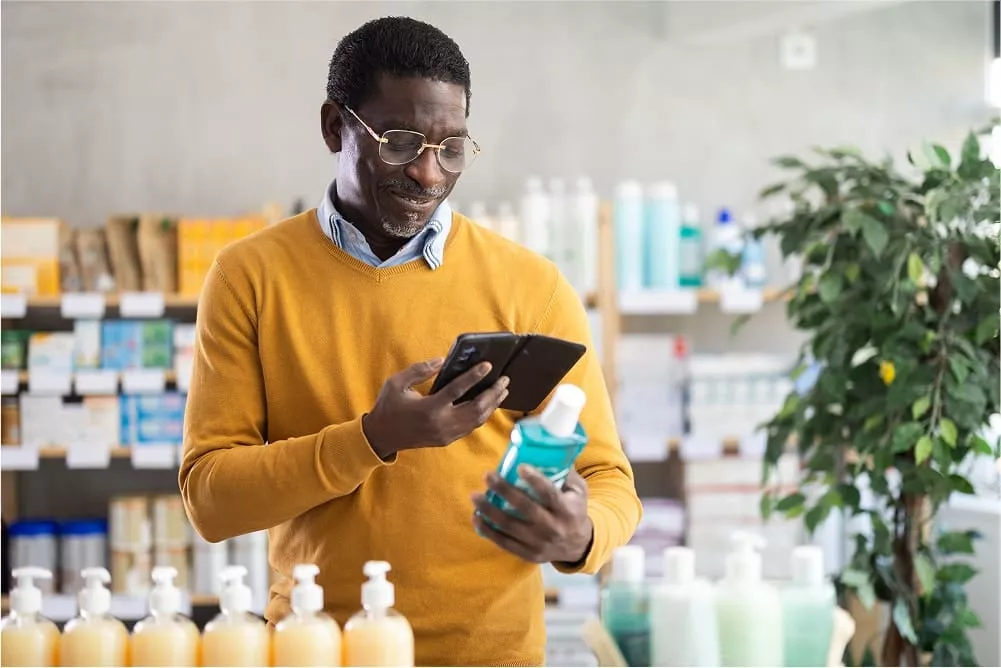
Our approach:
Sustainability is fundamental to the life cycle of our bio-based ingredients, which allow to make food and beverages safer, healthier and tastier, personal care formulations more natural and home care products greener, while limiting greenhouse gas emissions, supporting local agriculture and creating highly qualified jobs in and around our production sites.
Our progress:
Our ingredients produced by fermentation from locally sourced corn are mostly consumed in their region of origin and are fully biodegradable within days, limiting their environmental footprint over their whole lifecycle. They are intrinsically circular as the emitted at their end of life is the atmospheric CO2 absorbed months to decades before by the corn grown to produce them. Furthermore we continuously decrease the carbon footprint of our ingredients through the electrification of our production processes and the purchase and own generation of renewable energy. We aim to make them even more sustainable for the consumer through innovation and the support of regenerative agriculture.
Our impact
We believe the best things come from nature — so we work every day to preserve it for generations to come.
€300m
Investments in sustainability planned in the next five years
40%
We are targeting a 40% reduction in Scope 1 and 2 emissions by 2030
38%
Female representation in Executive Committee, up from 0% in 2020
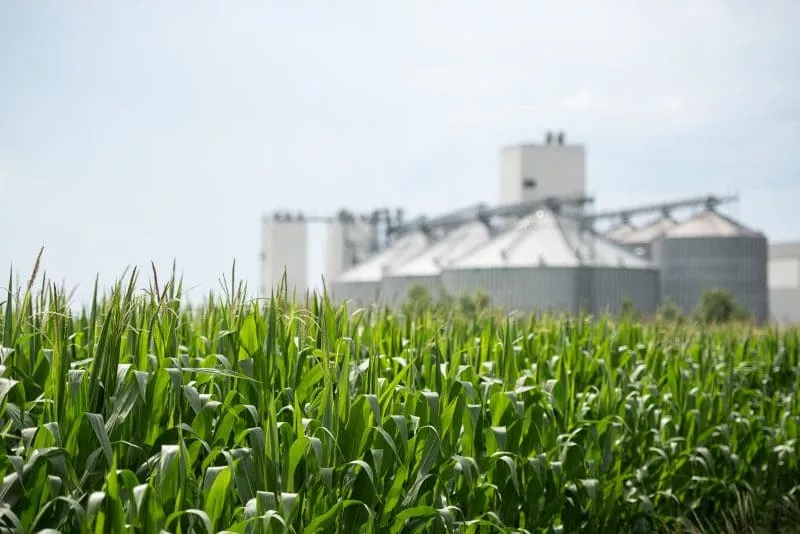
Sustainability report 2024 – Driving a greener future
Discover our commitment to sustainability through innovation, responsible sourcing, and carbon reduction. Our 2024 report showcases progress in renewable energy, waste reduction, and eco-friendly solutions, driving a greener future.
Our performance. Independently verified.
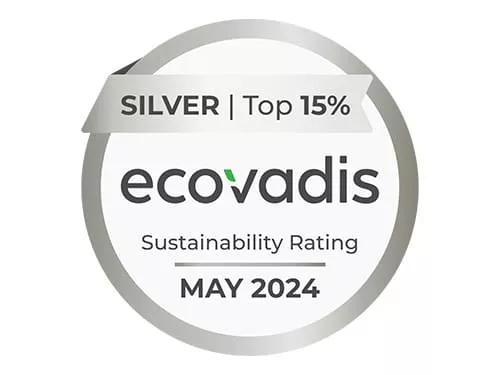
EcoVadis
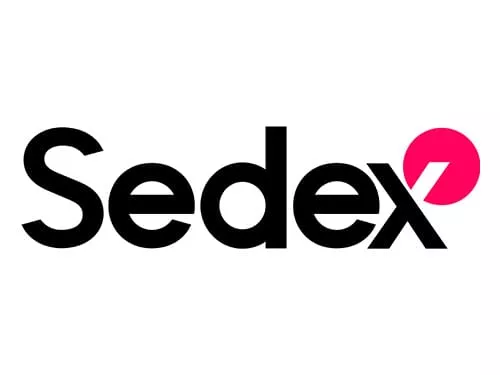
Sedex
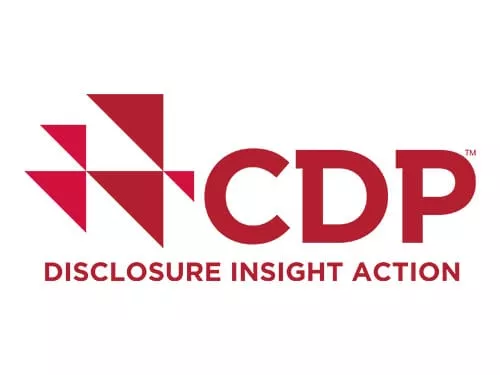
CDP
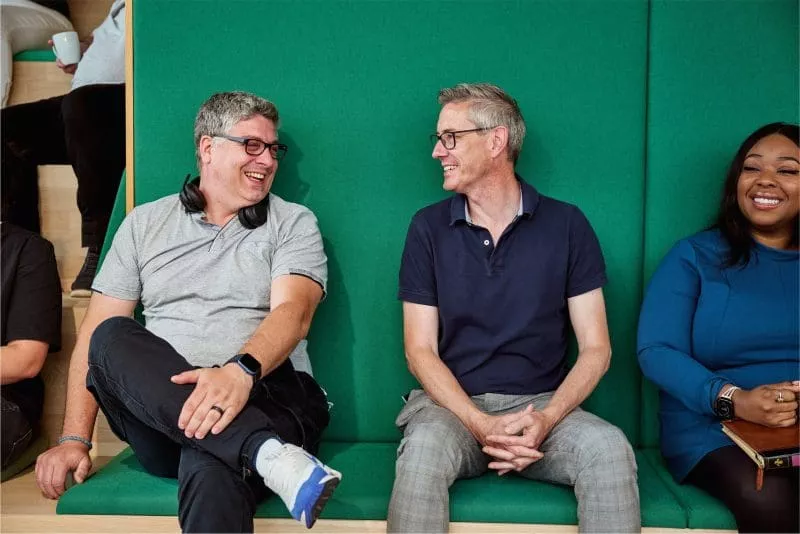
People
We prioritise the safety, health, well-being and development of our employees, business partners, consumers and communities while upholding the highest ethical standards and human rights across our operations and supply chain.
Planet
We are committed to reducing our environmental footprint by tackling climate change, improving water efficiency, preserving biodiversity, and embedding circular economy principles into our value chain.
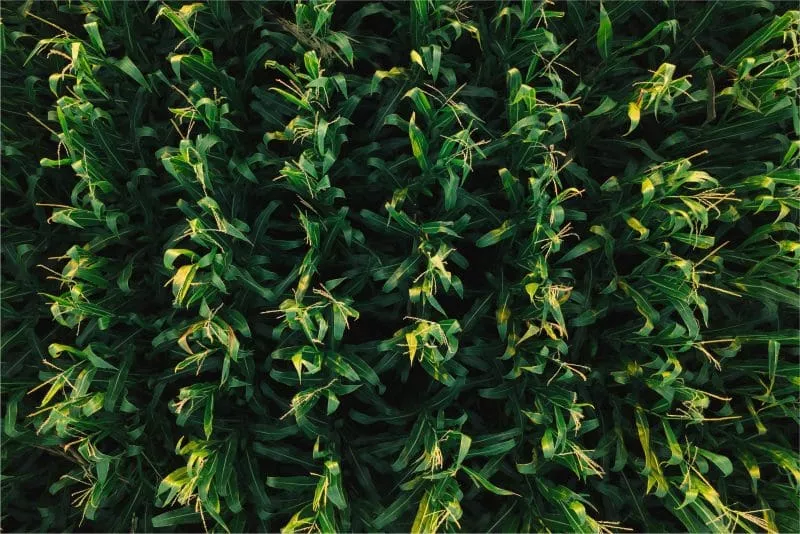
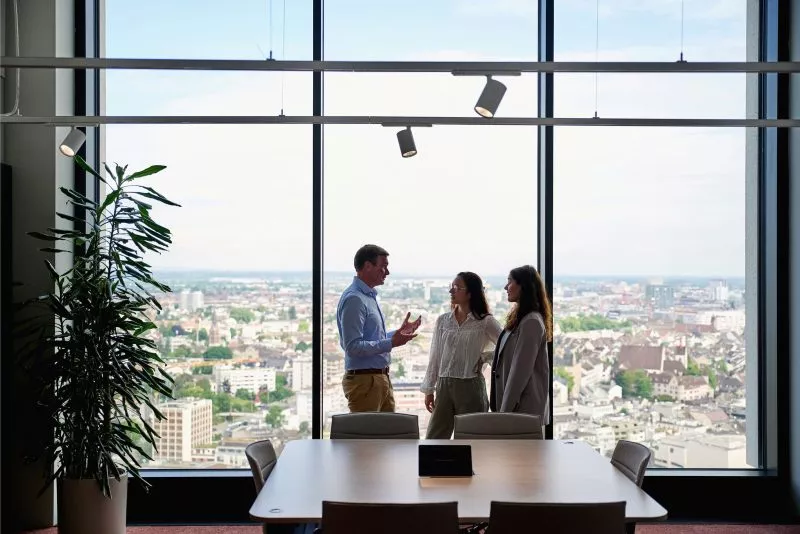
Integrity
We operate with purpose and integrity, creating a culture supporting our ambition, ensuring compliant and responsible business conduct, transparent governance, and sustainable supply chains while driving long-term value for all stakeholders.